Turbo-prop aircraft typically are louder – and exhibit significantly more vibration – than jet aircraft. In this particular case, the aircraft was being developed as a business aircraft, so it was extremely important that the turbo-prop noise and vibration be minimized. The key goal for the project was to achieve interior sound pressure levels similar to a typical jet aircraft.
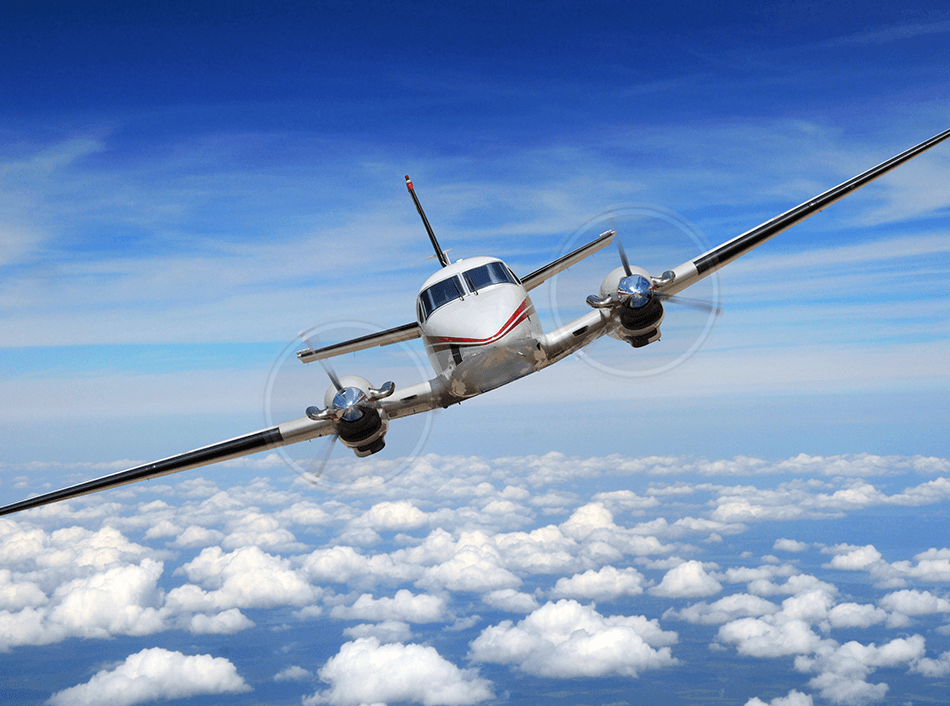
DTI designed and produced pre-cut kits consisting of an array of Tuned Vibration Absorber (TVA) units, which were then applied to a number of fuselage skin bays in the aircraft. The TVAs were located at approximately the center of the bay where bay stiffness is minimal and arrays were tuned for 2ndBPF effects. Each TVA weighed only 0.17 lb.
The TVAs were installed in tandem with a special DTI K1405 Standing Off Damping System, having a “tall” Stand-Off Layer which was also applied to the aircraft fuselage skin for enhanced stiffness (to minimize forced vibration from BPF events) and attenuation of turbulent boundary layer noise. The TVAs screwed onto a TVA mount (about the size of a U.S. quarter) that was bonded to the fuselage skin via quick-cure structural adhesive. The SODS parts were cut with an access hole for the TVA mount. The TVAs included a cover assembly designed to protect the TVAs from interference from thermal acoustic blankets or wiring harnesses, etc. in the aircraft.
The TVAs were injection-molded using a proprietary DTI VEM displaying very stable properties with respect to temperature. This approach ensured that the TVAs remain tuned as temperature fluctuates during the aircraft flight envelope.
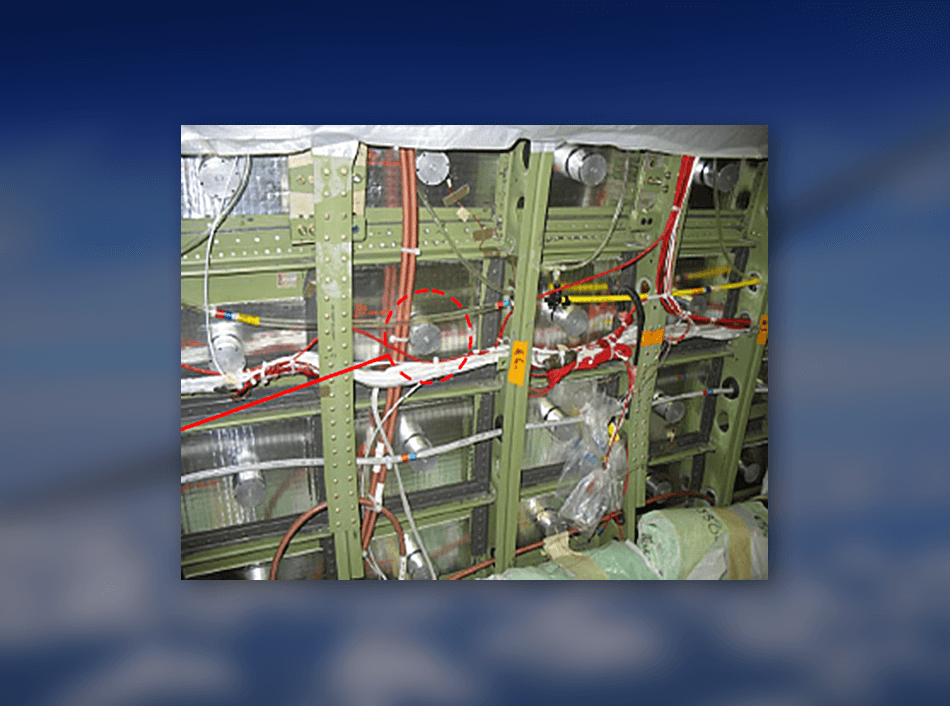
Sound pressure level goals for the aircraft were achieved. The TMD array yielded (-5 dBA) benefit for 2ndBPF @ 200 Hz. The SODS yielded (-3.0 dBA) benefit for TBL noise > 300 Hz.
Crucial to this project was DTI’s ability to economically manufacture the TVA units already-tuned, which alleviated the need for expensive manual tuning. DTI’s know-how in terms of VEM selection, control of the dynamic mechanical properties of our VEMs, as well as our understanding of adhesion and general manufacturing experience, resulted in a very successful countermeasure.
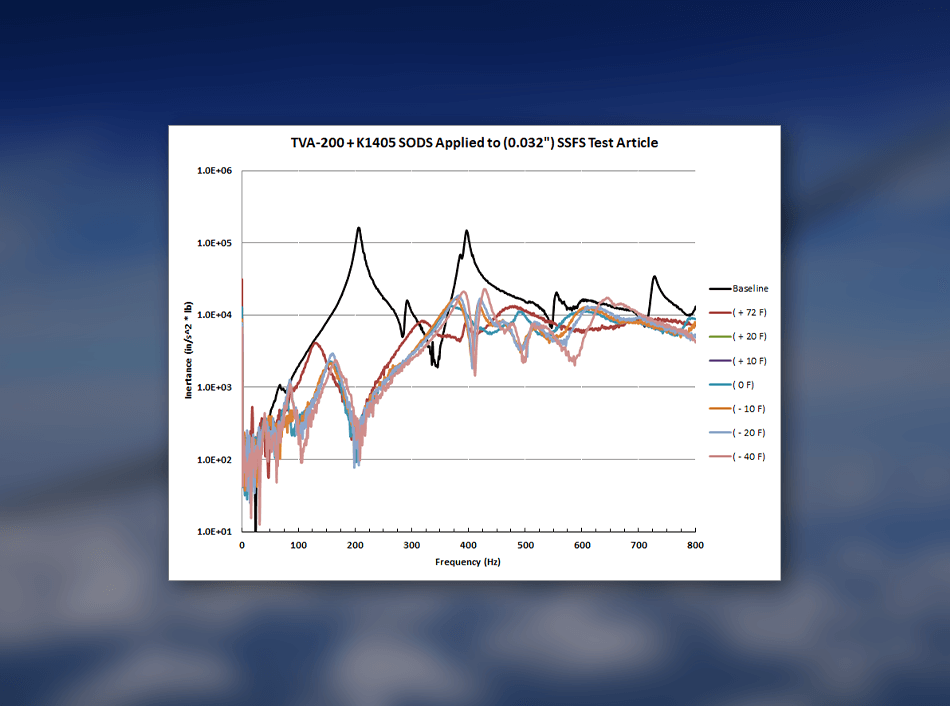