The customer contacted DTI regarding attenuation of resonance response of satellite structure near 120 Hz. Exposure to launch vehicle excitation and subsequent resonance response near 120 Hz jeopardized sensitive instruments aboard the satellite. Countermeasure installation sites were very limited, due to the large amount of instrumentation mounted to the the structure.
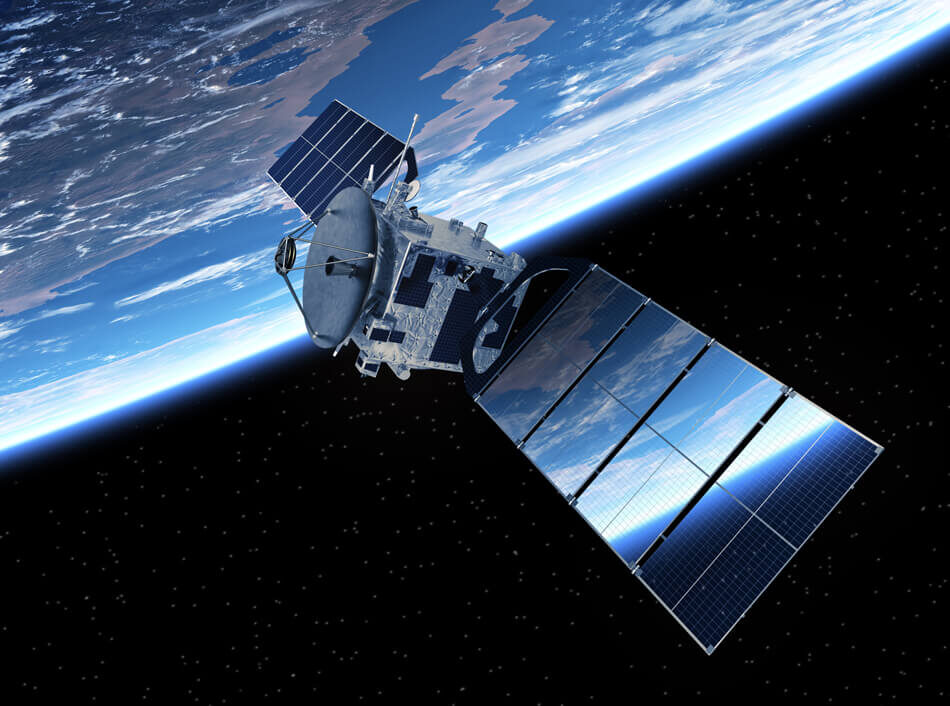
DTI configured an FEA model of the satellite structure and correlated model predictions to existing experimental data. Using the FEA model, DTI designed a pair of Tuned Mass Dampers (TMDs) countermeasures and determined best/viable installation sites. TMD mass was optimized using the FEA tool.
Viscoelastic material utilized in the TMD design was selected based on stable modulus vs. temperature performance (to maintain tuning frequency) and excellent outgas characteristics. An elevated temperature post-cure of the processed VEM enhanced outgas performance.
Significant effort was expended in design of the TMD mounting bracket. The TMD masses were constructed of tungsten carbide to minimize volume. Nevertheless, the TMD masses were required to hang out beyond the satellite framework, as this was the only available space for them. A challenge associated with the TMD mounting bracket was that it be kept low-mass as possible, but have adequate stiffness to transfer TMD dynamic actuation forces to the satellite framework structure (at the proper location). More effort went into the TMD mounting bracket design than into the TMD countermeasure concept itself.
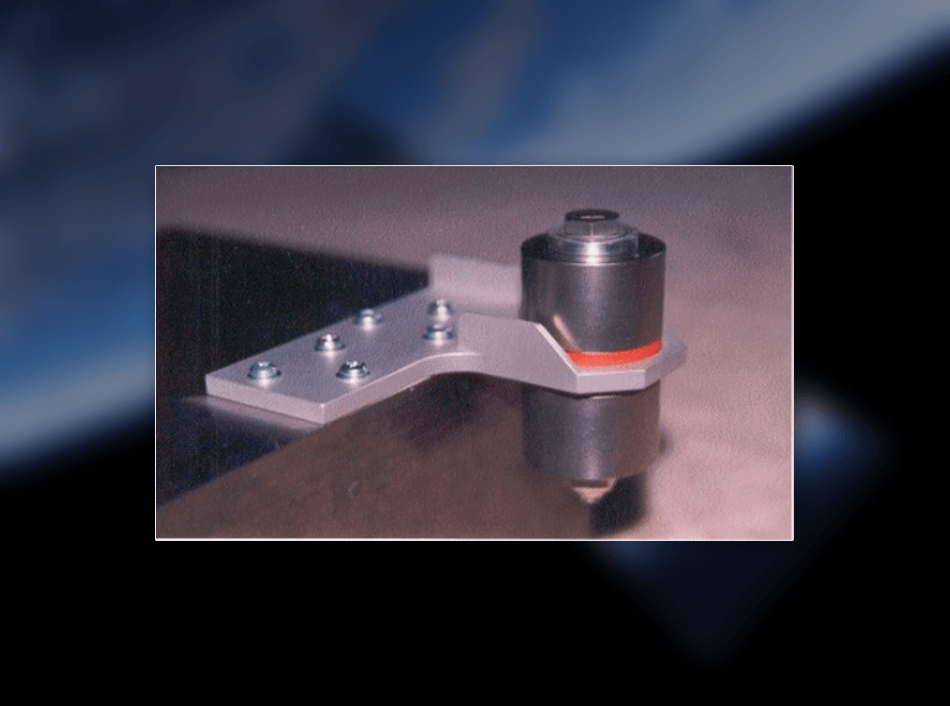
Application of the TMDs resulted in substantial reduction in resonance response of the structure for 120 Hz.
